Sandvik Coromant and Chalmers University of Technology teamed up to conduct experiments for increasing the product lifetime of metal cutting tools. With the help of the NanoMAX beamline at MAX IV, a team of scientists and R&D professionals will further study the atomic structure of the Titanium Aluminium Nitride (TiAlN) coatings.
What makes metal cutting tools durable is a thin layer of coating material. The thickness of this layer is only a tenth of the thickness of a human strand of hair, but still, these coatings are extremely hard. However, working under high temperatures and pressure, they can still be worn off.
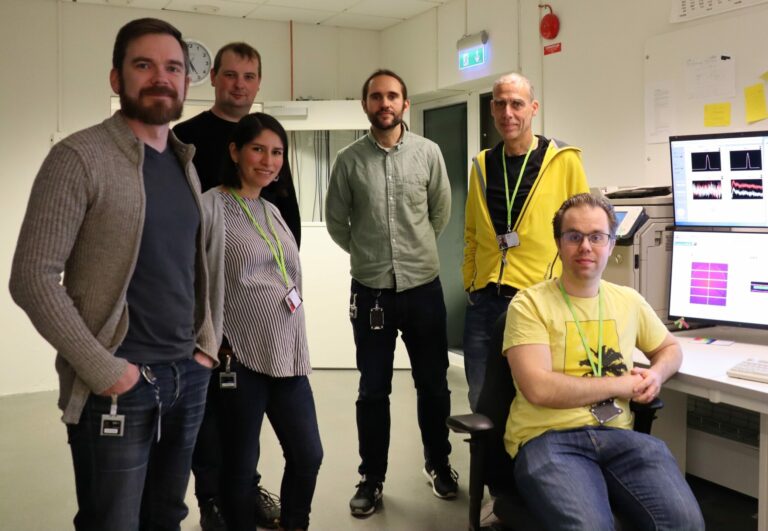
Sandvik Coromant and Chalmers University of Technology teamed up to develop a solution to make more durable coatings. Thus, the researchers are using various coatings as samples to study their structures and understand why some of them are more resistant to stress than others. The experiment is taking place at MAX IV because in-house measurements at this level are not possible at Sandvik Coromant.
While Fatima Pardo, a Research and Development Engineer at Sandvik Coromant, load samples to the beamline, another R&D Engineer from Sandvik Coromant, Linus von Fieandt, tells about the backstory of the experiment: “This is a Vinnova pilot project that encourages collaboration between industries and academia. We have applied for a grant to finance beamtime in this facility. To do so, we have come together with the Chalmers University of Technology as we have no hands-on experience in recreating experiments such as this.
Observation with 60 nm beam size
Magnus Hörnqvist Colliander, a Senior Researcher at the Chalmers University of Technology, dived into the specifics of the experiment, explaining how this research is beneficial for the industry. “Not all coatings have a long lifespan. The lifetime depends both on the structure of the coatings (how the atoms are arranged) and on the internal stresses built into the coating during its production. The company aims to study the structure and properties of the coatings to produce more durable coatings in the future. This knowledge will decrease the production costs and contribute to sustainability as fewer tools used also means that less material is used to make them.”
With the help of nanoscopic observation techniques available at MAX IV, it is possible to study structure and stress levels in these coatings at the correct size regime. Since the beam size at the NanoMAX beamline at MAX IV is 60 nm, it is possible to perform diffraction experiments with high enough spatial resolution to measure the phase composition and stress gradients through the thickness of the coating. It is worth mentioning that traditional measurements provide information about the coating’s average stress and atomic arrangement. Thus, all the information about variations through the thickness is lost. This is the exact information essential for understanding the relationships between the processing conditions and the final performance of the coating.
“By comparing these observations with the measured performance of the different coatings, we can find out whether the samples with a certain structure or a certain stress profile are more long-lasting than the others,” says Colliander. He mentions that the experiment’s findings are essential for Sandvik’s product development in the future.
Sandvik Coromant is not the only user in the metal industry to take advantage of MAX IV. To learn more about other industrial users and their experiments, check MAXESS Industry Arena for more cases or contact us.