Metal cutting tool company Seco Tools and researchers from Linköping University have studied structural changes in TiAlN coatings on tools in atomic detail at the MAX IV beamline Balder. The results will guide the company's development of more efficient metal-cutting tools.
Metal machining – the art of manufacturing shapes in different types of metal – requires high-performance cutting tools. Such tools must have excellent wear properties and also be able to cut metals fast to increase the production rate.
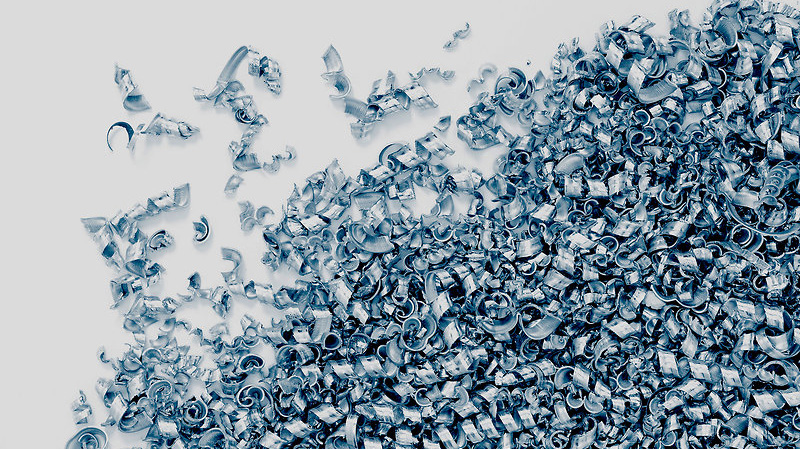
A TiAlN coating (consisting of titanium, aluminium, and nitrogen) on the cutting tools offers high resistance to heat and oxidation. However, the tools are still subject to decomposition during machining.
To develop cutting tools that can better withstand wear and tear, tool producers want to understand the wear behaviour by studying the decomposition processes in atomic detail.
Using XRD techniques (X-ray diffraction), it is possible to characterise structural changes that happen across the surface of the cutting tools when being used, but detecting the initial stage of decomposition in the local chemical environment requires other methods.
Studying changes in the atomic structures using Balder beamline
To get high spatial resolution information on how coating selection impacts the tool’s performance through small, local changes in the atomic structures of the tool’s coatings, Seco Tool’s research team used X-ray absorption spectroscopy techniques (XANES and EXAFS) at the Balder beamline at MAX IV.
Cobalt-toughened cemented carbide inserts coated with a TiAlN compound were prepared as samples. Each contained a different aluminium content.
The study showed that changes in the atomic content of the surface could be detected. The changes, including a change in experienced temperature across the tool surface and a variation in the coating response to this increased temperature, also varied depending on the aluminium concentration.
“The high temperatures, up to ~1000°C, and pressure, more than 1GPa, that our tools are exposed to during metal cutting requires very resistant and durable materials. Through this experiment, we were able to detect chemical changes that we have not studied before”, explains Jon Andersson, R&D Expert PVD at Seco Tools.
“Also, the very high spatial resolution data enabled us to track changes within the local area worn during the processing.”
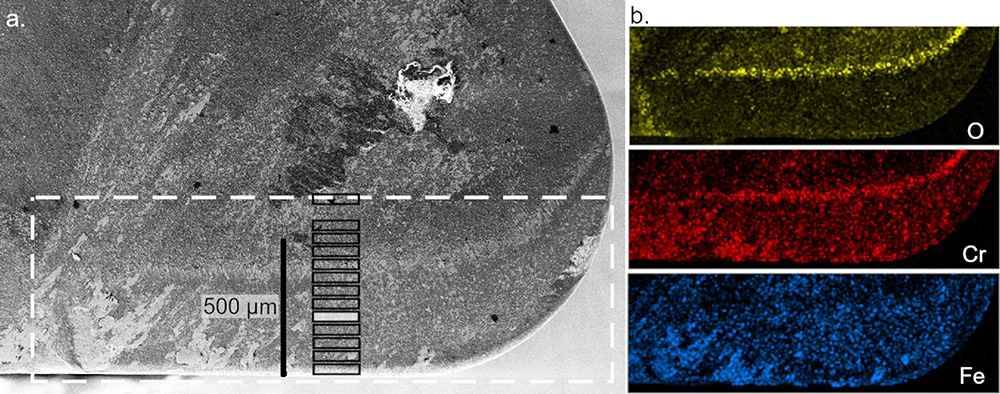
“New ideas for improving the materials”
The results have been published in Applied Surface Science Journal and will guide Seco Tools’ development of more efficient and optimised tools.
“This study is an important puzzle piece for understanding how the materials decompose. It gives us new ideas for improving the materials”, says Jon Andersson.
Read the full case at MAXESS Industry Arena: Improving metal cutting tools using X-rays.
Publication
Interested in conducting industrial experiments at MAX IV? Contact our industry office!