Your car gets hit by another vehicle, and the steel in its construction is deformed by the impact. The steel isn't just designed to be strong enough to protect you. It also gets stronger because of the impact. It all has to do with the different arrangements that the atoms inside the steel can assume and under which conditions these so-called phases can exist.
In a recent experiment at DanMAX beamline, researchers from Tampere University deformed steels using a specially designed mechanical test setup. They investigated the effects of the deformation speed on the phases that the steels would assume during deformation. The steels used in the experiments were commercial so-called Transformation induced plasticity or TRIP steel and metastable austenitic stainless steels.
“The phase transformations have not been studied in this way before,” says professor Mikko Hokka. “There have only been slow or incremental studies that do not fully reflect the dynamics of an actual impact. With our experiment, we can study the rate or speed of the phase transformation at different loading speeds.”
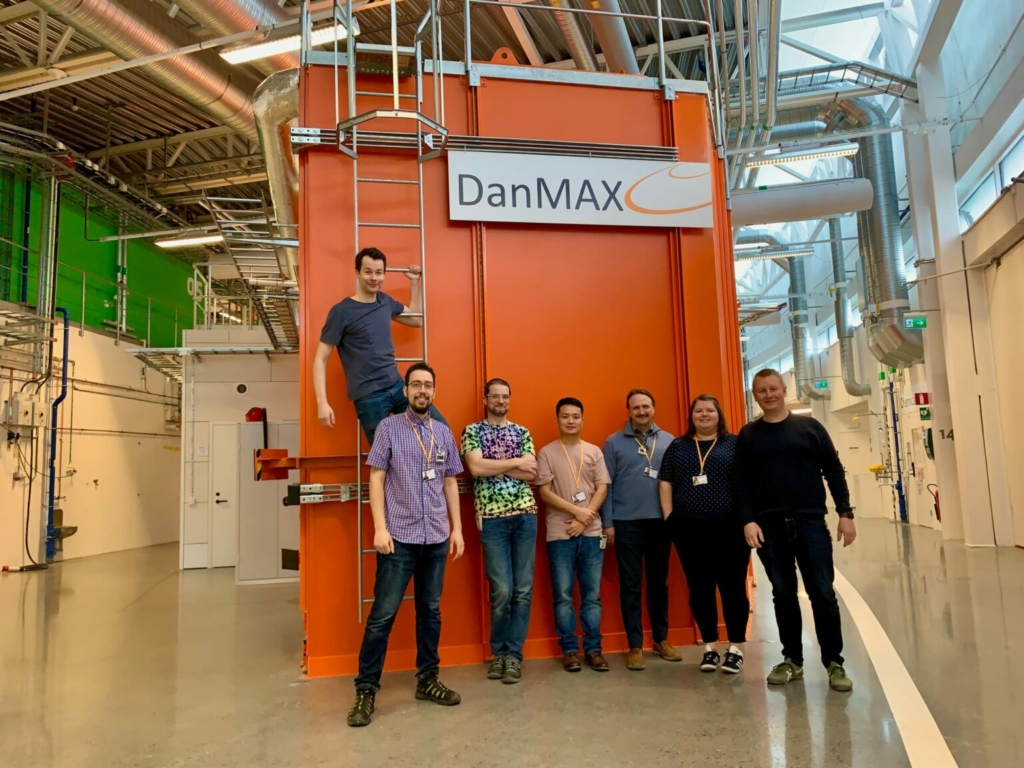
When deformed fast, the steel gets hot because of adiabatic heating, which changes the structure and properties of the material. Before the deformation, the steel exists at least partly in the austenite phase that transforms to strong martensite as it deforms. This phase transformation is affected by the loading speed and the adiabatic heating.
“The beam at the DanMAX beamline is intense enough to pass through the steel sample so that we could investigate the phase changes in real-time while being pulled by the mechanical loading rig,” professor Hokka continues. “The device itself is far from trivial to make and was designed in collaboration with the DanMAX staff and the supplier.”
To keep the beam on the same spot of the sample during the experiment, the researchers had to design a test rig with two fast motors pulling the specimen at the opposite ends to make sure that the motor actions were synchronised.
The researchers were a bit overwhelmed by the amount of data they acquired during the experiment.
“We learned much more than we expected setting up the experiment,” concludes professor Hokka. “We’d like to try other kinds of steels and start thinking about how they could be improved for the next generation of materials. We would also like to express our gratitude for the help and support from the DanMAX team before and during the experiment.”