To develop longer-lasting metallic materials for harsh operating conditions requires understanding of their surface composition, structure and properties. A Swedish research group investigated the surface chemistry and thickness of the protective native oxide layer of nickel superalloys at MAX IV’s FlexPES beamline.
Synchrotron X-rays today remain largely underutilized in corrosion science, a field which examines the degradation of engineering materials. Known hurdles to industrial research on commercial alloys include a lack of availability for beamtime and complex, unfamiliar methods of data analysis for new users, among others. The current study demonstrates the exciting possibilities of X-ray measurements at lightsources like MAX IV.
“We were able to show that even so-called minor alloying elements may contribute significantly to the thin oxide film that is protecting the material from corrosion. This is important knowledge for intelligent alloy design,” explained Alfred Larsson, the author and PhD student at Lund University (LU). The project is coordinated by LU professor Edvin Lundgren and KTH professor Jinshan Pan.
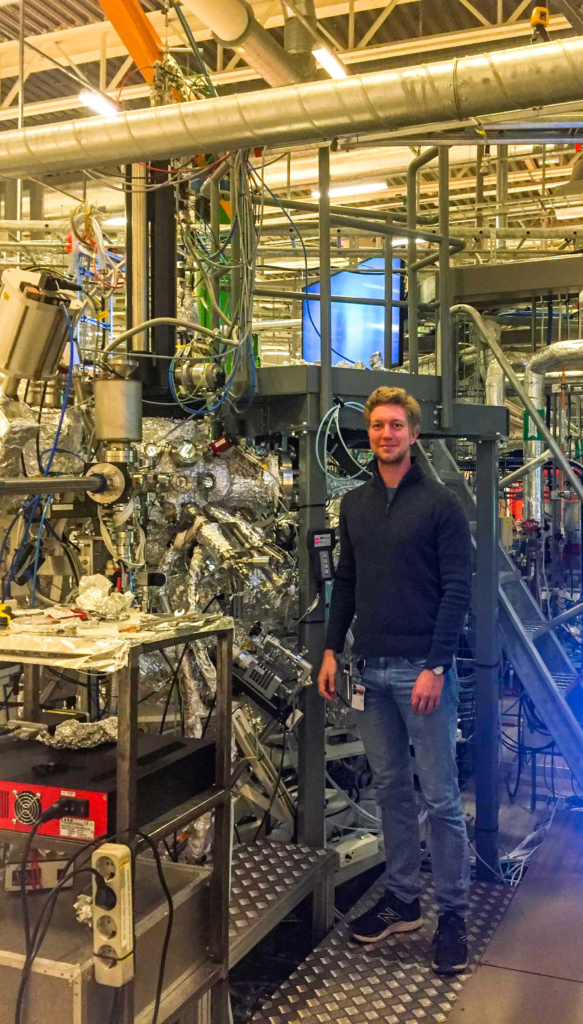
Superalloys are metallic materials that can withstand high temperatures, mechanical stresses, or oxidizing environments over long periods. Whereas the chemistry and structure of native oxide films are known to strongly influence the lifespan of industrial metallic materials, knowledge of these oxides on superalloys is relatively limited.
X-rays reveal reasons for durability
The research collaboration from KTH Royal Institute of Technology, Lund University, and Sandvik Materials Technology, aimed to elucidate the surface chemistry and thickness of the native oxide and hydroxide layer of industrial-grade nickel alloys: 59, 625, and 718. Ex situ measurements of surface composition and density were taken using X-ray Photoelectron Spectroscopy (XPS) with ultrahigh vacuum at MAX IV’s FlexPES beamline by scientist Alexei Preobrajenski, and X-ray Reflectivity (XRR) under atmospheric pressure and ambient conditions at the Swedish Materials Science beamline P21.2 at PETRA III at DESY in Germany. The experiment was carried out remotely due to the Covid-19 pandemic.
The two techniques employed are complementary. XPS reveals the chemical nature of the native oxide and subsurface layer of the alloy and is used to calculate the thickness of the oxide and hydroxide layer. XRR measures the thickness and electron density of the different surface layers.
The analysis revealed the differences between alloys, the preferential oxidation, and enrichment of alloying elements in the surface oxide films. This knowledge will advance our understanding of the differences in corrosion resistance between the alloys studied, explained Larsson. Further, the data for oxide composition aligns with thermodynamic principles, that is, the enthalpy of formation can explain which alloying element predominantly contributes to the oxide film.
The use of synchrotron X-rays for studying surfaces and thin films of applied materials has robust, beneficial aspects. “The main benefits of synchrotron radiation are the tuneable energy and high flux, allowing careful calibration and calculation of the chemical composition and thickness of very thin surface oxide or hydroxide films,” said Larsson. Other strengths include enhanced beam stability and coherence, and energy resolution of the sample, as compared to lab-based X-ray sources.
The group plans for future studies on how surface oxide film changes under realistic corrosive conditions. Two potential paths include investigation of electrochemistry with ambient-pressure XPS at MAX IV’s HIPPIE beamline and X-ray absorption at BALDER beamline.